Caso prático: A eletroerosão por fio como alternativa para a maquinação de ranhuras em discos de turbinas para o setor aeronáutico.
ONA levou a cabo um estudo para analisar o processo de eletroerosão de corte por fio (WEDM) como alternativa à maquinação convencional (brochagem) de ranhuras de discos de turbina para o setor aeronáutico.
\ A eletroerosão na maquinação de ranhuras em discos de turbinas no setor aeronáutico
Só é possível ser líder do setor da Eletroerosão se existir um trabalho contínuo de investigação de novas tecnologias e aplicações, para oferecer soluções avançadas adaptadas às necessidades dos clientes. A ONA é um claro exemplo de uma empresa orientada para a inovação. O seu percurso de 65 anos oferece as melhores tecnologias à eletroerosão garantem-no. De acordo com esta filosofia, a empresa basca levou a cabo um estudo para analisar o processo de eletroerosão de corte por fio (WEDM) como alternativa à maquinação convencional (brochagem) de ranhuras de discos de turbina para o setor aeronáutico. De facto, no futuro, a eletroerosão por fio de ranhuras de discos de turbina poderia converter-se numa opção industrial viável à brochagem.
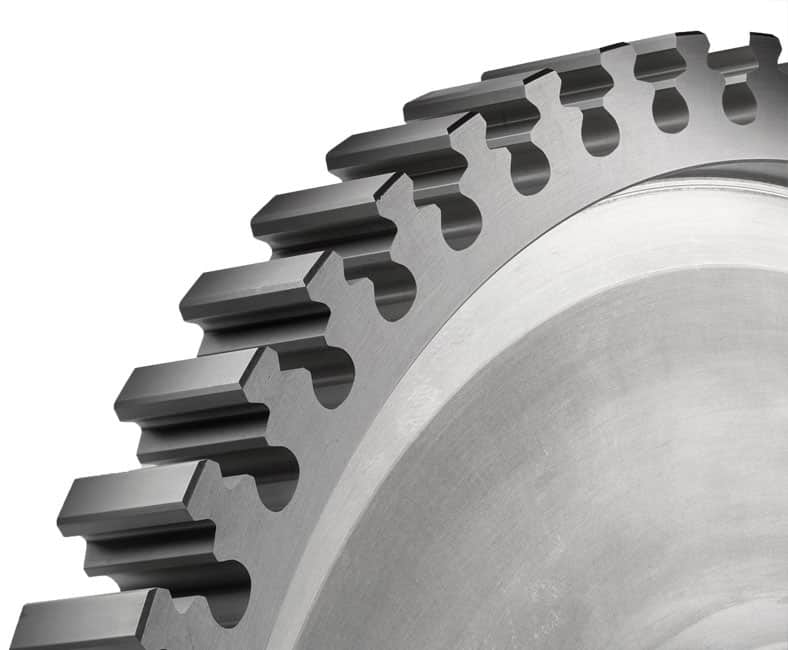
\ Pressuposto e método
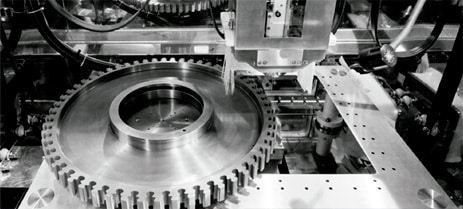
Ena sua investigação, a ONA comparou o processo de eletroerosão com as maquinações mais tradicionais, como por exemplo a brochagem e a fresagem. Como pontos fundamentais da investigação, a ONA comparou parâmetros como os requisitos de integridade superficial, precisão e tempo de maquinação das ranhuras de inserção de pás.
Para o teste, cortou-se um disco de turbina com as seguintes características:
Para la prueba se ha cortado un disco de turbina con las siguientes características:
• Material: Inconel 718.
• Diâmetro Exterior: 350 mm.
• 28 ranhuras.
• Ranhuras de disco de turbina num ângulo de 30 graus.
• 82 mm de espessura.
• Tolerância de perfil 0,01 mm.
• Tolerância de posicionamento angular radial 0,08 mm.
O objetivo da investigação é cortar, através da tecnologia de eletroerosão de corte por fio, os dentes do firtree da turbina, cumprindo os requisitos de tolerâncias e, desta forma, analisar a seguinte informação:
• Tempo de desbaste de um perfil completo.
• Tempo de acabamento de um perfil completo.
• Tempo total de erosão de um perfil completo.
• Tempo total do desbaste do disco de turbina (incluindo o tempo de preparação).
• Tempo total do acabamento do disco de turbina (incluindo o tempo de preparação).
• Tempo total de maquinação (incluindo o tempo de configuração).
• Taxa de remoção de material MRR (mm2/min).
• Espessura da camada de material refundido.
\ Configuração e condições de maquinação EDM
Para realizar a análise aplica-se uma tecnologia standard da ONA para a liga de níquel, uma mesa giratória de 2 eixos e duas condições de limpeza diferentes. Por um lado, boas condições de lavagem (boquilhas fechadas) e, por outro lado, piores condições de limpeza (boquilhas abertas). Além disso, utiliza-se um fio revestido de 0,25 para o corte de desbaste.
Os dois cenários escolhidos para o estudo (boquilhas abertas e fechadas) permitem realizar diferentes testes para avaliar adequadamente o tempo de erosão, já que este depende em grande parte das condições de limpeza. Por vezes, as características geométricas dos discos de turbina impedem o uso da eletroerosão com boquilhas fechadas.
\ Resultados da investigação.
Após a realização dos testes, os resultados demonstraram que com a tecnologia de eletroerosão por fio é possível obter uma espessura da camada refundida no intervalo de mícrones necessário (cerca de 5 µm) e com precisão suficiente nas ranhuras de inserção de pás, dentro da tolerância de 0,01 mm. Estes resultados obtiveram-se após uma passagem de desbaste e duas passagens de acabamento (estratégia de 3 cortes).
Em piores condições de limpeza (boquilhas abertas), a taxa de remoção de material para o desbaste é de 110 mm2/ min. De facto, para a estratégia utilizada na investigação (uma passagem de desbaste e duas passagens de acabamento), a taxa de remoção de material é de 60 mm2/ min.
Por sua vez, com boas condições de limpeza (boquilhas fechadas) verifica-se uma melhoria relevante da taxa de remoção de material. Só para o desbaste, tinge mais de 400 mm2/ min.
\ Comentários baseados nos resultados obtidos.
A maior parte dos discos da turbina têm perfis de ângulo entre 5 e 30 graus. A função do corte cónico da máquina de eletroerosão de fio da ONA obtém bons resultados na precisão geométrica para perfis de menos de 10 graus. Para ângulos maiores, recomenda-se uma mesa giratória de dois eixos.
Para conseguir a eliminação de material desejada e melhorar os tempos de maquinação é fundamental a limpeza do dielétrico na área de erosão. É essencial manter a maioria das boquilhas fechadas no perfil. Para discos de turbina de menor diâmetro (quando as boquilhas interferem com o dispositivo de fixação), recomenda-se o uso de boquilhas especiais.
Por último, aconselha-se também a utilização de fios revestidos para reduzir o processo da eletroerosão por fio, especialmente no corte de desbaste.
\ Conclusões
Depois desta investigação, é possível concluir que a eletroerosão por fio de perfis de discos de turbina é uma alternativa bastante válida para competir com a brochagem enquanto solução industrial no setor aeronáutico. Os geradores de última geração, cada vez mais potentes, e os controlos numéricos mais avançados permitem otimizar o tempo de maquinação e reduzir a espessura da camada branca. Além disso, asseguram uma precisão geométrica muito boa. No estudo realizado pela ONA (estratégia de 3 cortes), a maquinação de ranhuras de discos de turbina cumpre as tolerâncias geométricas, alcançando uma camada branca inferior a 5 μm. Para além disso, obtém-se informações muito importantes sobre a taxa de remoção de material e o tempo de maquinação. É verdade que a certificação do processo completo de maquinação por eletroerosão, de acordo com os standards aeronáuticos, pode ser um processo longo e dispendioso. Por essa razão, a ONA chegou à conclusão de que a melhor opção é a combinação da eletroerosão por fio para desbaste, por ser mais rápida e económica, com a brochagem com vista ao acabamento final. Desta forma, a recertificação do processo não é necessária.