A nossa estratégia é oferecer às empresas da área da aeronáutica máquinas de Eletroerosão personalizadas com elevado valor acrescentado
ENTREVISTA COM MARIUS PETEAN, GESTOR DE CONTAS CHAVE NA ONA
\ Máquinas personalizadas e de elevado valor para o setor aeronáutico
O desenvolvimento de novos geradores digitais inteligentes tem sido o pprincipal impulsionador para a EDM se tornar num processo de fabrico viável e altamente competitivo na indústria aeroespacial, mesmo para as chamadas ‘peças críticas’, ou seja, peças rotativas ou as que suportam cargas cíclicas e podem estar sujeitas a falha por fadiga. A ONA desempenhou um papel importante nesta evolução positiva, tendo feito contributos como a máquina por fio AV35 para o fabrico de firtrees de discos de turbinas.
Conforme referido nesta entrevista com o Gestor de Contas Chave na ONA Marius Petean, o futuro implica continuar a investir fortemente num setor que já representa 25 % do volume de negócios anual da empresa. “As mais importantes empresas do setor aeroespacial utilizam máquinas da ONA. O nosso objetivo comercial é continuar a crescer dentro dos próprios clientes, nas unidades de produção que têm espalhadas por todo o mundo, bem como nos fornecedores de 1ª e 2ª linha que utilizam máquinas EDM, com especial ênfase no mercado Norte-Americano”, refere Petean.
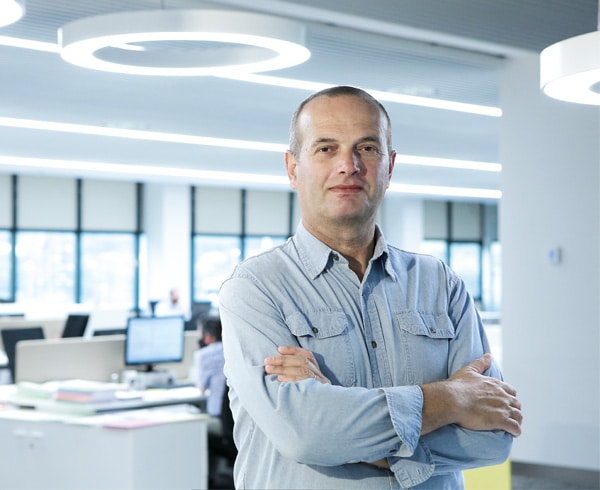
PERGUNTA. Como é que a ONA começou a desenvolver aplicações para os setores energético e aeroespacial?
RESPOSTA. A ONA está envolvida em projetos da indústria aeroespacial há mais de 20 anos. Mas durante muito tempo, operava num âmbito limitado. Tratavam-se de clientes que necessitavam de máquinas capazes de satisfazer determinados requisitos tecnológicos associados com processos de maquinação EDM de componentes de turbinas a gás. Há apenas 10 anos, a faturação relativa a empresas aeroespaciais representava menos de 5 % do volume de negócios anual da ONA. No entanto, constatámos há não muito tempo que existia uma necessidade de recentrar a gestão de um setor que pudesse aumentar as vendas e, ao mesmo tempo, compensar e complementar outros setores de negócio tradicionais, como por exemplo, os moldes e a estampagem para a indústria automóvel. Esta nova abordagem teve início há 6 anos. Desde então, o volume de vendas relativo ao setor aeroespacial não parou de crescer e representa hoje 25 % da faturação total, perspetivando-se um aumento significativo nos próximos anos.
P. Poderá dizer-se que a EDM é já a tecnologia de eleição para o fabrico de determinadas peças de geometria complexa num setor tão exigente como o aeroespacial? Encontra-se ao nível da brochagem e fresagem em termos da qualidade do produto final?
R. A EDM foi considerada um ‘mal necessário’ na indústria aeroespacial. Existem determinados componentes que só podem ser maquinados com a ajuda de EDM. Por esse motivo, os designers de peças aeroespaciais desenvolveram procedimentos de definição de conceção específicos para estes componentes que incluem requisitos processuais de EDM, para além de requisitos de aceitação em matéria de qualidade superficial e metalúrgica. EDM é considerado um processo especial que necessita de ser aprovado antes de ser aplicado à produção em série. No entanto, esta perceção tem vindo a mudar nos últimos anos. Por um lado, as novas tecnologias EDM baseadas em geradores digitais de vanguarda permitem agora um acréscimo substancial de remoção de material e, por outro lado, um aumento considerável da qualidade da superfície erodida. A EDM continua a ser um ‘mal necessário’, mas é agora considerada uma alternativa industrialmente viável para substituir ou complementar outros tipos de maquinação. Por exemplo, a qualidade superficial que a EDM por fio pode atingir atualmente faz deste processo uma alternativa válida para substituir a brochagem de discos de turbina.
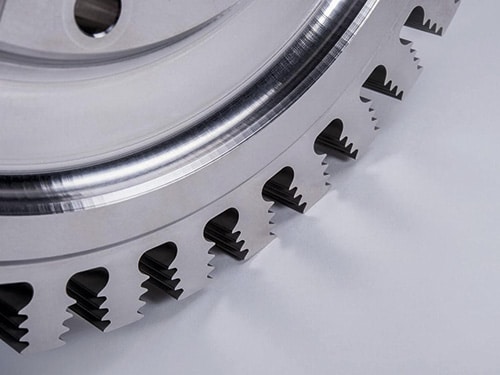
Alguns exemplos recentes incluem a máquina por fio AV35 da ONA para o fabrico de firtrees de discos de turbinas.
P. De que tipos de peças/aplicações estamos a falar?
R. A gama de componentes e aplicações aeroespaciais passíveis de processamento por EDM é cada vez maior. Enquanto antigamente existia apenas um número reduzido de aplicações, quase exclusivamente do âmbito da EDM tradicional, tais como furos e ranhuras de arrefecimento em NGV, segmentos e pás, estas diversificaram-se agora, tendo passado a incluir impulsores, IBR, OGV, discos de turbina, câmaras de combustão e pás de ventiladores.
P. O que provocou este salto nos últimos anos? Foi meramente o desenvolvimento de novos geradores que transformou a EDM numa técnica de maquinação competitiva para o setor aeroespacial, mesmo no que se refere às chamadas ‘peças críticas’?
R. Obviamente, o salto tecnológico deu-se com as novas gerações de geradores de máquinas EDM, mas também por avanços no desenvolvimento da tecnologia EDM. Enquanto que anteriormente eram poucos os parâmetros de EDM que podiam ser configurados, agora podem ser usados 30 parâmetros configuráveis. Isto proporciona uma flexibilidade muito maior quando se trata de encontrar uma solução ideal. Há ainda que reconhecer o trabalho desenvolvido pelos fabricantes de equipamento original (OEM) para introduzir a EDM em peças críticas, bem como a motivação e tenacidade dos gestores de engenharia e produção, que se mostraram abertos e preparados para aceitar, verificar e aprovar EDM para este tipo de peças. Sem eles, teria sido impossível chegar a este ponto.
P. Quais são as vantagens técnicas trazidas pelos novos geradores ao fabrico EDM de, por exemplo, discos de turbinas a gás, peças rotativas que atingem até 60.000 rpm e têm de ser capazes de resistir a flutuações de pressão e temperaturas extremas?
R. No caso dos novos geradores ONA, foi o facto de serem digitais. Passa a ser possível desenvolver novas tecnologias EDM, tal como a eletrólise, bem como diminuir ou mesmo eliminar microfissuras, obtendo-se níveis de camada refundida muito baixos de apenas alguns mícrones. Os requisitos de superfície são aceitáveis e as peças podem ser aprovadas para a aviação.
P. Quais são as vantagens que a EDM tem para oferecer ao fabrico de peças do setor aeroespacial comparativamente com técnicas mais tradicionais, tais como a brochagem e fresagem?
R. De um ponto de vista industrial, foram definidas algumas vantagens muito interessantes, em particular relacionadas com a EDM por fio. Quando comparados com a maquinação convencional com recurso a brochagem e fresagem, os custos recorrentes com materiais consumíveis são substancialmente mais baixos. No que se refere à brochagem, a EDM oferece soluções de prototipagem rápidas e económicas. Entre conceção e fabrico, uma ferramenta de brochagem poderá necessitar até um ano, enquanto que a EDM por fio é quase que imediata e está diretamente associada à programação do perfil de corte. Além disso, nesta abordagem não há margem para erros; se por algum motivo a ferramenta de brochagem não estiver correta, é necessário modificar a conceção e fabricar uma nova. No caso da EDM, após o corte da peça, o perfil é medido e tem de ser ajustado, o que pode ser feito diretamente através da programação da trajetória de corte. Por outro lado, a autonomia da máquina de EDM por fio é outra grande vantagem. Todos os modelos AV da ONA têm a opção de usar um sistema de bobina de fio de 45 kg, que é quase 8 vezes superior a uma bobina standard com 8 kg. E quando se trata de EDM por penetração, observamos uma tendência para a automação com recurso a robôs e armazenamento partilhado ou individual de elétrodos.
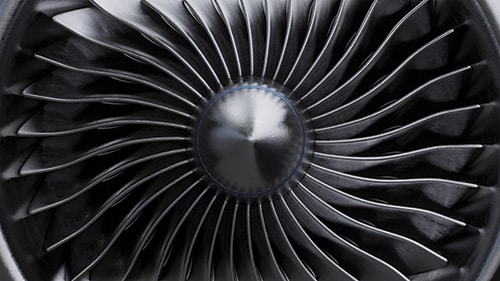
P. Os métodos de maquinação tradicionais possuem limitações que a EDM não possui quando se trata de realizar determinadas geometrias ou processar determinados materiais?
R. EDM é um processo de maquinação sem contacto. Exige apenas que os materiais a erodir possuam condutividade elétrica. Obviamente, isto representa uma vantagem relativamente à maquinação convencional. Quase não existe diferença entre a remoção de material e o desgaste da ferramenta (elétrodo) em caso de erosão de ligas de alumínio ou níquel, muito ao contrário da maquinação convencional.
P. Que papel desempenhou a ONA nesta evolução para transformar a EDM na técnica de eleição para o fabrico de peças aeroespaciais?
R. Trabalhamos em colaboração com os nossos clientes no sentido de encontrar soluções de maquinação específicas para os seus componentes. Todas as soluções que procuramos para os seus problemas recorrem a EDM. Digamos que estes exercícios de abordagem dão origem a soluções interessantes e muitas vezes surpreendentes.
P. Então a ONA produz soluções personalizadas e à medida para as empresas.
R. Exatamente. A nossa estratégia no setor consiste em oferecer aos clientes soluções com elevado valor acrescentado. Ouvimo-los e oferecemos-lhes soluções personalizadas de acordo com os seus requisitos e o seu grau de familiaridade com a EDM. Por exemplo, um cliente com pouca experiência em EDM solicita-nos uma solução chave-na-mão que inclui a conceção e o fabrico de ferramentas, tecnologia EDM, programação NC (Controlo Numérico) e aprovação de peça industrial. Dois números de peças distintos e, no total, nove operações EDM diferentes.
P. Quais foram as aplicações/contribuições mais recentes da ONA para o setor aeroespacial?
R. Alguns exemplos recentes incluem a máquina por fio AV35 para o fabrico de firtrees de discos de turbinas da ONA; máquinas de EDM por fio para o corte automático de perfis aerodinâmicos para encaixar pás em anéis; EDM por penetração com remoção de material de elevado rendimento; EDM por penetração adaptada a cavidades complexas em componentes como impulsores; ou EDM por penetração para furos moldados em pás e NGV.
P. Referiu que a ONA já atribui 25 % do seu volume de vendas atual ao setor aeroespacial, mas qual é a previsão para o futuro?
R. As principais empresas do setor aeroespacial utilizam as nossas máquinas. O nosso objetivo é continuar a crescer em conjunto com os nossos clientes, nas unidades de produção que têm espalhadas por todo o mundo, bem como com os fornecedores de 1ª e 2ª linha que utilizam máquinas EDM, com especial ênfase no mercado aeroespacial Norte-Americano.
P. Onde são de esperar as próximas inovações em equipamentos EDM para o setor? Quais são os desafios seguintes para mostrar que a tecnologia EDM é mais atual do que nunca no que se refere ao fabrico de peças aeroespaciais?
R. As tecnologias e os procedimentos estão em constante inovação. Novas aplicações de EDM surgem na sequência do desenvolvimento e da introdução de novas tecnologias. Um exemplo revelador disto é a EDM para o corte de peças fabricadas através da produção aditiva. No futuro, não só necessitaremos de tecnologias adaptadas, mas também de máquinas diferentes e mais bem adequadas ao tipo e tamanho das peças de produção aditiva. Um desafio maior será a cibersegurança de máquinas num ambiente industrial digital e conectado. E um valor acrescentado importante para clientes/utilizadores de máquinas EDM será a recolha de dados da máquina e do processo para análise subsequente, de forma a melhorar os processos de fabrico e a manutenção preventiva das máquinas.